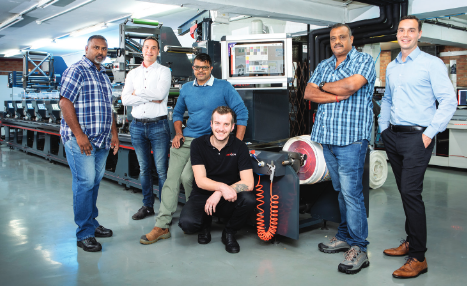
Rotocon director Pascal Aengenvoort explained that feedback from narrow-web industry customers prompted the company to broaden its market offering by developing and manufacturing a cost-efficient ECOLINE-branded flexographic press that balances registration accuracy with high running speeds.
Flexing new R&D skills to meet market demands, GTV Label Master, a Durban-based label converter, recently invested in South Africa’s first Rotocon ECOLINE RFP 340 flexo printing press, and a complementary ECOLINE Pro Mount platemounter.
‘After working with Rotocon for many years, and successfully using its ECOLINE slitting, inspection and rewinder systems and digital printed label converting and finishing systems, it was a no-brainer for us to invest in the RFP 340 flexo press,’ commented GTV Label Master’s factory manager, Collin Naidoo.
According to Naidoo, the flexo press was running immediately thanks to the simplicity of its design and the ease-of-operation, which enabled the operators to adapt easily. The press features Yaskawa’s latest servo drive and control system, while each printing unit is driven by a separate servo motor. These units are designed for optimal ink transfer and pressure adjustment to guarantee crisp-dot printing in high line counts, text, linework, solids, adhesives and varnishes. If fine-tuning is required, it can be done quickly, by adjusting the corresponding pressure setting device on both sides.
‘The BST web inspection system also ensures high-quality during the printing process,’ said Aengenvoort. The lightweight aluminium print cylinders feature a high-precision helical gear transmission for high accuracy. ‘This design ensures that installing the cylinder in the printhead is a smooth and easy operation,’ he noted. The LED-UV curing system ensures an improved energy footprint across the short web path. The filmic material isn’t affected by the UV curing temperatures during printing, thanks to a water chiller system linked to the impression cylinder. The unwind unit is equipped with a corona treater, dust-cleaning unit and static system to ensure maximum printing stability.
Naidoo explained that investing in the RFP 340 and the Pro Mount at the same time has eliminated the need for making brackets to use on existing plate mounters. ‘The RFP 340 requires a different way of mounting plates and the Pro Mount, which is also user-friendly, enables mounting of flexo plates on different cylinders, without having to change brackets.
‘The after-sales support we receive from Rotocon has always been at the highest standards, plus spare parts are readily available, which helps prevent any downtime,’ stated Naidoo. ‘Working with Aengenvoort is also a major benefit for our team because of his knowledge of the KwaZulu-Natal market and his commitment to ensuring that everything runs smoothly,’ concluded Naidoo.
ROTOCON
+27 11 397 2172
http://www.rotocon.co.za